PROJEKT HORTEN IV
FORTSCHRITTSBERICHT DEZ-2024
Nach dem Neustart des Horten IV Projekts im Jahr 2023, welches überwiegend von vorbereitenden Maßnahmen geprägt war,
brachte das zurückliegende Jahr 2024 deutliche Fortschritte auf dem langen Weg zum Erstflug.
Beplankung des Außenflügels
Zum Jahresbeginn 2024 war das Flugzeug gewogen, die Rudermomente bestimmt, die Steuerung vermessen und von Dr. Fritz Kießling
(ehemaliger Mitarbeiter am DLR-Institut für Aeroelastik in Göttingen) eine erste Flatterrechnung durchgeführt.
Auf Basis der Ergebnisse seiner Berechnungen konnten wir die Entscheidung treffen, die Außenflügel nicht mit dem im Original
verwendeten Magnesiumblech zu beplanken, sondern mit Blech aus einer neuartigen Aluminiumlegierung, welche eine günstigere
Verarbeitbarkeit und Korrosionsbeständigkeit aufweist.
Vom DLR in Göttingen erhielten wir Anfang des Jahres auch die Zusage, den für die Zulassung geforderten Standschwingversuch
zur Flatteranalyse dort durchführen zu können.
Als Termin hierfür wurde uns "das Ende des dritten Quartals 2024" genannt. Damit gab es eine klare Zeitvorgabe für die Fertigstellung des Außenflügels.
Bei der Akaflieg planten wir, die notwendige Umformung des Bleches im Nasenbereich mit einer selbstgebauten Vorrichtung vorzunehmen.
Hierzu wurden erste Versuche durchgeführt, die schnell zeigten, dass das profilgenaue Biegen des Aluminiumbleches mit dem erforderlichen
engen Nasenradius auf einer Länge von über 2 Metern nicht einfach werden würde.
Froh war man daher über das Angebot einer versierten, externen Firma, sowohl die Umformung als auch die Vernietung der Beplankung
mit Holm und Rippen zu übernehmen.
Eine weitere Voraussetzung für den geplanten Standschwingversuch war eine funktionsfähige Steuerungskinematik.
Dafür mussten die noch fehlenden Steuerungsteile für den Außenflügel gefertigt werden und deren abschließende Montage erfolgen.
Die Aluminiumbeplankung sollte ursprünglich bis Ende Juli 2024 fertiggestellt sein. Leider gab es hier Verzögerungen, und der
Fertigungstermin wurde immer wieder verschoben.
Als die Aluminiumbeplankung nicht rechtzeitig fertig zu werden drohte, und der Termin in Göttingen bedenklich näher rückte, fiel die Entscheidung,
nun doch die von Prof. Dr.-Ing. Schürmann ausgelegte CFK-Schale zu bauen und aufzukleben. Aufgrund der bevorstehenden Urlaubszeit von Dennis Patzig
war jetzt Eile geboten. Noch vor Dennis Urlaub wurden beide Flügelschalen auf den vorhandenen Formen gebaut.
Ende August 2024 wurden die CFK-Schalen angepasst, zugeschnitten und gefüllert.
Auf den Außenflügel entfällt ein wesentlicher Teil der Flügelschränkung, die durch das Verkleben von CFK-Schale und Rippenstruktur nicht
verfälscht werden durfte.
Da die Holm-Rippen-Struktur ohne Beplankung noch sehr torsionsweich war, wurde diese fest auf dem Frästisch aufgespannt und genau ausgerichtet.
Die CFK-Flügelschale wurde mit 3M Scotch-Weld™ EC-9323 aufgeklebt, einem in Luft- und Raumfahrt erprobten Zweikomponenten Epoxy-Klebstoff. Bei einem
"Trockenversuch" stellte sich heraus, dass es, auch mit vielen Händen, nicht möglich war, die Schale weit aufzubiegen und zu positionieren, ohne
dabei den Kleber abzustreifen. Um genau dies beim Aufsetzen auf die Rippen-Holm-Struktur zu verhindern, wurde eine Hilfskonstruktion gebaut, mit der
sich die CFK-Schale möglichst weit aufspreizen ließ.
Anschließend erfolgte das Auftragen des Klebers auf Rippen und Holm.
Die mittels der Hilfskonstruktion aufgespreizte CFK-Schale wurde an der Wurzelrippe des Außenflügels zunächst an einem Drehpunkt fixiert und dann
vorsichtig herunter geschwenkt.
Die Hilfskonstruktion wurde vorsichtig entfernt, um ein abruptes Zurückschnellen der aufgespreizten CFK-Schale zu vermeiden.
Die CFK-Schale wurde mithilfe von Clecos in ihrer Position fixiert und zusätzlich eine Pressung im Bereich des Holms angebracht.
Eine abschließende Kontrolle bestätigte, dass an den Verklebestellen ausreichend Kleber hervorgequollen war, als Zeichen einer vollflächig gelungenen Verklebung.
Da nur
ein planer Tisch zur Verfügung stand, konnten die beiden Außenflügel nur jeweils nacheinander mit der zugehörigen CFK-Schale verklebt werden.
Die vielen aufeinanderfolgenden Arbeitsschritte erforderten ein gutes Zeitmanagement und bedeuteten einen enormen Zeitaufwand für alle Beteiligten,
um den Termin in Göttingen zu halten. Hierfür vielen Dank.
Mit dem fertigen Torsionsverbund des Außenflügels konnte die Ansteuerung der Steuerflächen am Außenflügel erstmals richtig eingestellt und erprobt werden.
Für den Versuch in Göttingen waren die Außenflügel nun bereit.
Parallel zur Fertigstellung der Außenflügel erfolgten die Vorbereitungen für den Standschwingversuch.
Um die Zeit in Göttingen bestmöglich für die Versuchsdurchführung nutzen zu können, wurden bereits in Darmstadt die Positionen für
die spätere Anbringung der Beschleunigungssensoren ausgemessen und markiert.
Standschwingversuch beim Institut für Aeroelastik des DLR
Nachdem alle Vorarbeiten rechtzeitig abgeschlossen werden konnten, wurde das Flugzeug zum Strukturdynamiklabor nach Göttingen transportiert,
dort aufgebaut und final mit den Sensoren instrumentiert und verkabelt.
Der Versuch fand vom 23. September bis zum 1. Oktober 2024 statt.
Die Flatterrechnung auf Grundlage der im Versuch ermittelten Modelparameter wird derzeit im Rahmen eines Advanced Design Project (ADP) an der
TU Darmstadt unter Federführung von Tim Posekardt durchgeführt.
Bei der aeroelastischen Untersuchung der Horten IV liegt ein besonderes Augenmerk auf dem für Nurflügelflugzeuge typischen "Body-Freedom-Flutter",
bei welchem die Nickschwingung mit der ersten symmetrischen Flügelbiegung koppelt. Eine möglichst genaue Ermittlung der Starrkörper-Nickform war daher
von großer Bedeutung. Zu den Versuchsbedingungen gehörte deshalb auch ein entsprechend authentischer "Ballast" im Cockpit.
Im Bild unten ist ein üblicherweise im Rahmen von Automobil Crash Tests verwendeter Dummy zu sehen, in der für die Horten IV spezifischen liegendknienden
Piloten-Position. Die Firma BGS Böhme & Gehring GmbH hatte diesen freundlicherweise für die Dauer des Standschwingversuchs zur Verfügung gestellt. Auf
diese Weise konnte die Massenverteilung eines späteren Piloten und damit auch das Massenträgheitsmoment um die Nickachse realitätsnah abgebildet werden.
Im Hintergrund sind Fritz Kießling und Jan Schwochow (DLR) zu sehen.
Die letzten Schritte zur Fertigstellung der Horten IV umfassen die Randbögen der Außenflügel, die zusätzliche Vernietung der CFK-Beplankung, die Abdeckung der
Störklappen (Seitensteuer) sowie die Lackierung der Außenflügel.
Die inzwischen fertiggestellte Aluminiumbeplankung eröffnet die Möglichkeit für den späteren Bau eines originalgetreueren Außenflügelpaares.
Vor dem Erstflug muss abschließend der komplette Zulassungsprozess beim LBA durchlaufen werden.
Im Sinne von Professor Bernd Ewald danken wir allen, die das Vorhaben, erneut eine Horten IV in die Luft zu bringen, bisher unterstützt haben.
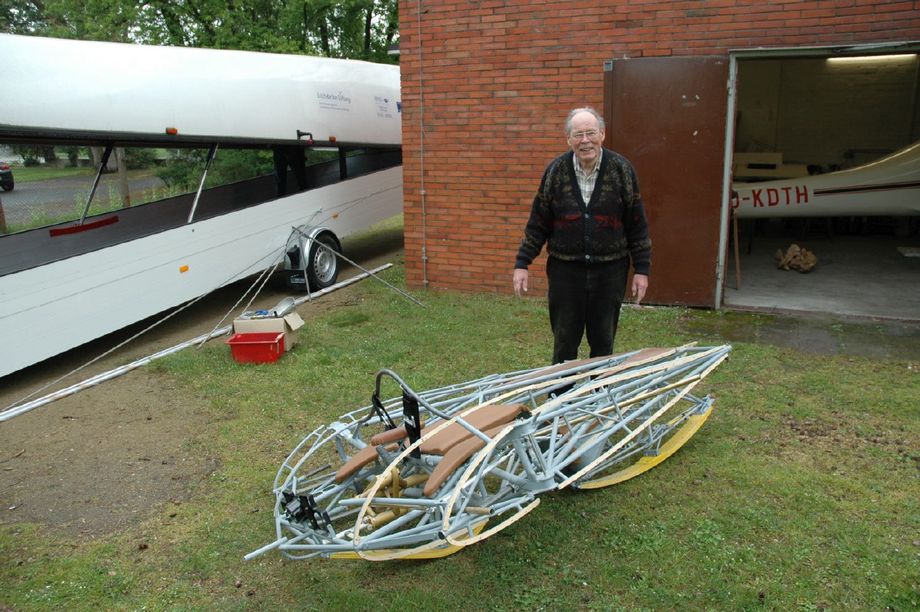
Prof. Dipl.-Ing. Bernd Ewald im April 2009
Besonderer Dank in diesem Jahr gilt dem Deutschen Zentrum für Luft- und Raumfahrt für die Zusage, den Standschwingversuch der Horten IV beim DLR
Institut für Aeroelastik in Göttingen zu realisieren und dem beteiligten DLR-Team um Jan Schwochow und Fritz Kießling für die Unterstützung und
Durchführung des Versuchs.
Unterstützt wurde die Fortsetzung des Projekts auch durch das Fachgebiet für Strömungslehre und Aerodynamik unter Leitung von
Frau Prof. Dr.-Ing. Jeanette Hussong.
Nicht zuletzt gilt der Dank dem großen Engagement der Akaflieg Darmstadt und dem Kernteam "Horten IV-Projekt".
Darmstadt, 7. Dezember 2024
Felix-Kracht-Stiftung
Der Stiftungsvorstand Martin Stenger
Sponsoren der Felix-Kracht-Stiftung:
Blomberger Holzindustrie
Schichtholz für Hauptholm
Tennant Metall u. Technologie GmbH
Spezialstahl für Beschläge
Lehrwerkstatt Deutsches Zentrum für Luft- und Raumfahrt
Bau des Rippensatzes, Fräsen der Formklötze für die Sperrholznase
BUKO-Ferrodur
Vergütung Hauptbeschläge
Röder Präzision
Schweißen der Beschläge
Erich-Becker-Stiftung (FRAPORT)
Finanzielle Zuwendungen
Traditionsgemeinschaft "Alte Adler" e.V.
Finanzielle Zuwendungen
Akaflieg Darmstadt
Bau der Hauptholme
Lehrwerkstatt Lufthansa Technik AG
Bau des Mittelteils
Deutsche Lufthansa AG
Finanzielle Zuwendung
FAG Kugelfischer
Alle Kugellager
Alexander Schleicher Flugzeugbau
Stoßstangenführungen
Schempp-Hirth Flugzeugbau
Stoßstangenführungen
Tost Flugzeuggerätebau
Schleppkupplungen, Bugrad
Karl Abhau
Fluginstrumente
Wolfgang Krauss
Finanzielle Zuwendung
Vintage Glider Club, Deutsche Sektion
Finanzielle Zuwendung
Winter Bordinstrumente
Bordinstrumente
Gadringer Gurte GmbH
Gurtzeug
Heinrich Mertens
Fallschirm
Josef Weiss Plastic GmbH
Cockpit-Verglasung
Becker Flugfunkwerk GmbH
Funkgerät
Deutsches Segelflugmuseum mit Modellflug
Finanzielle Zuwendung (Vermächtnis Heinz Scheidhauer)
Air Avionics
Air Com Funkmodul und Air Control Display
TU Darmstadt; Fachgebiet Strömungslehre und Aerodynamik
Wissenschaftliche und materielle Unterstützung
Deutsches Zentrum für Luft- und Raumfahrt Institut für Aeroelastik
Durchführung des Standschwingversuchs
Ralf Kaiser
Materialspende
Stahl Aircraft & Materials GmbH
Materialspende
Kasaero GmbH und Kaelin Aero Technologies GmbH
Metallumformung mit Materialspende
BGS Böhme & Gehring GmbH
Dummy-Leihgabe für den Standschwingversuch
Ungeachtet der großen Bemühungen unserer Sponsoren bei der Unterstützung des Projektes fehlen für die erfolgreiche Beendigung
des Projektes noch finanzielle Mittel.
Die Felix-Kracht-Stiftung bittet daher alle Freunde der Horten IV um Spenden für dieses Projekt! Die Felix-Kracht-Stiftung ist berechtigt,
Spendenbescheinigungen auszustellen.
Unser Dank gilt an dieser Stelle allen Sponsoren, auch den vielen hier nicht im Einzelnen genannten Personen, für jede Art von Spenden,
für wertvolle fachliche Anregungen und für eine engagierte Beteiligung.
Ohne die zahlreichen Beiträge der Unterstützer ließe sich dieses ambitionierte Vorhaben nicht realisieren.